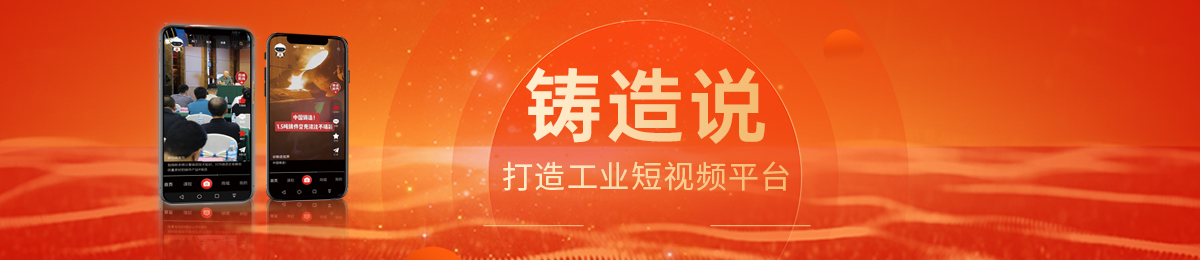
您好, 欢迎来到百铸网! 热线电话:400-8088-177 企业邮箱:[email protected] 注册|登录
2016-02-29来源:暂无数据
1、 夹砂形成机理: 当砂型中浇入金属液,在型腔尚未充满和金属液尚未凝固时, 一方面,金属液对型腔表面砂层热作用,砂型表面层温度急剧上升,因而表面层受热急剧膨胀,产生热应力;另一方面,砂型表面层产生的水蒸气通人砂型内部时,被冷却而凝聚在表面干燥层的下面,成为水分饱和凝聚薄层。此层热温强度很低,仅为正常状态湿强度的几分之一。由于石英膨胀 热应力的作用,迫使表面层有沿着水分凝聚层滑动而拱起的趋势。此时,金属液尚未充满,金属液的压力作用迟于表面层的拱起开裂。砂型开裂后,当金属液从破裂处侵入冷却凝固后,就形成夹砂。
2、 水玻璃砂不易形成夹砂的机理: 水玻璃型砂,在低温时,由于铸型的刚体性质,不能吸收膨胀,产生的应力就大;相反,在具有大膨胀量的高温下,由于铸型显示出粘弹性的性质,在某种程度上可以吸收膨胀,所以应力小。因为水玻璃砂具有这种加热后,开始时膨胀,但是随后就收缩的特性,故不易产生夹砂。
3、 夹砂形成的原因分析: CO2水玻璃砂不易形成夹砂,为什么产生夹砂呢? 从夹砂形成的机理可以看出,在以石英砂颗粒为骨干的铸造条件下,型腔表面砂层的热膨胀和铸型内的水分迁移是形成夹砂的外因。砂层膨胀造成的热应力是表面拱起的动力,砂层的容让变形能力和层与层之间的连接强度是表面拱起破裂的阻力。从这个意义上讲,夹砂产生的原因是摇枕、侧架浇口侧热作用强,型砂热膨胀大,容让变形能力差,表面砂层与里层的连接强度不足和型砂中水分高(铸型吹干不足)。 从夹砂形成的时期看,在铸型尚未充满的时期。从这个意义上讲,夹砂产生的时期与铸型的吹干程度有紧密的联系:吹干不透,干强度差,砂型容易缩短夹砂发生临界时间, 从发生夹砂缺陷的情况看,夹砂发生在浇口引入处的平面距离型腔界面较近的表层或较深层,说明金属液的热作用强,型砂的热膨胀大。这主要取决于原砂的化学组成的性质和粒度的级配。同时,铸型在二氧化碳硬化时,透气性差,脱水不好,水分含量较高,强度不足;透气性不好,导热性差,水分饱和凝聚区离铸型界面很近或较近,易缩短夹砂临界时间。
二、 生产中防止CO2水玻璃砂夹砂采取措施:
1、 减轻热膨胀,延缓夹砂时间,提高容让能力方 面
(1) 采用膨胀系数小的原砂,即选择好的砂源。主要从砂源 化学组成、粒度和粒度级配上提高容让能力,选较粗的原砂。原来用50/100原砂,改为用40/70原砂,效果明显。
(2) 降低浇注温度,采取快的浇注速度,以减少热强度和过 热时间。原来浇注速度28秒~38秒,现在浇注速度25秒~35秒。
(3) 避免大平面处于水平浇注,斜浇或者尽量让大平面远离 内浇道过热区。摇枕、侧架采取改内浇道引入位置,由上面改在侧面,工艺较复杂,效果不明显。
(4) 控制型砂的紧实度,在造型机造型的条件下,进行两次 补充紧实,有一定的效果。
2、 提高铸型连接强度,迁移水分饱和区远离型壁方面
(1) 型砂适当增加水玻璃的含量,控制合适的水分,以提高 干强度。水玻璃加入量由7%,提高到8%。
(2) 造型增加面砂厚度。一通过厚度增加,提高铸型的有效 强度壁厚;二使含水量高的背砂远离型壁,水分饱和区也相应远离型壁。面砂厚度由原来的30~40毫米,增加到50~100毫米。
(3) 铸型二氧化碳吹硬,在罩内装电热板加热。一通过加热 和二氧化碳联合硬化提高铸型强度;二通过联合硬化,降低铸型的型壁水分,水分越少,夹砂临界时间越长,抗夹砂能力增强。同时,吹硬时,扎好通气孔,更有利于提高硬化强度,降低型壁硬化层水分。工艺措施上要求吹气罩内加电热板,铸型上有足够的通气孔。
(4) 型砂中增加促硬成分,以提高铸型整个面砂部分的硬化 强度,同时,改善溃散性。在面砂中,加入有促硬成分的改性剂0.5%。
(5) 在大平面上插钉子,刷涂料,增加连接强度。原工艺措 施要求浇口侧大平面插钉子、刷涂料。
(6) 改善背砂的强度和透气性,以满足保证面砂的需要和改 善吹硬效果,同时,改善铸型的导热性。在一定的时期更换背砂,用30/50粗砂。
友情链接 友链交换添加QQ:2694467624 其他问题请咨询网站客服