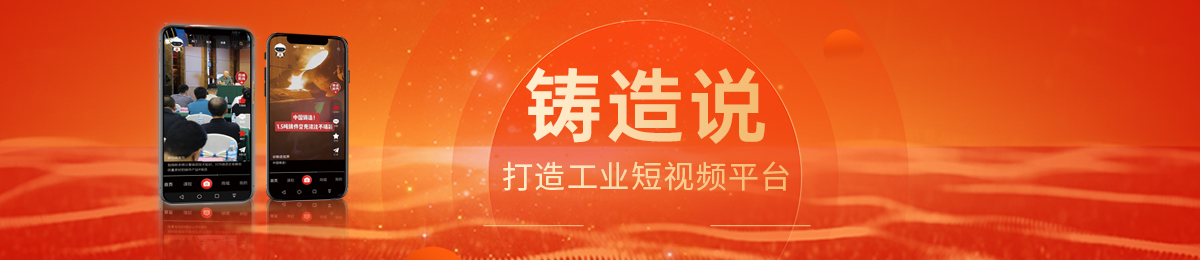
您好, 欢迎来到百铸网! 热线电话:400-8088-177 企业邮箱:[email protected] 注册|登录
2021-12-14来源:暂无数据
简述了发动机缸盖类铸件、轮类铸件、框架类铸件、泵壳阀类致密性铸件等几种典型铸铁件采用将铸件分割置于上、下型的做法,甚或是铸件全部设置于上型的工艺方案,分析了其容易导致气孔、浇不足、冷隔、缩孔、缩松、错边等铸造缺陷的原因。采用铸件全部设置于下型的工艺方案后,因其具有型腔排气充分、可优化设计浇注系统、可优化设置冒口系统、铸件错箱缺陷少、铸件加工余量少等优点,生产实践表明,采用此工艺后铸件合格率大幅提高,可获得内部组织更加致密、外形更加美观的高品质铸件。
几种铸件常用铸造工艺的不足
分型面位置(设在铸件中部与设在铸件顶面)的选择极为重要地影响着铸件合格率的高低、造型的难易程度等。笔者认为:砂型铸造生产中结构完全设置在下型的铸件,其铸件的造型、下芯、合型操作较为简便,铸件合格率较高。在铸造生产实践中,确实有很多类型的铸件的浇注位置本可以实现铸件结构全置于下箱,上型只须设置铸件的浇冒口等工艺结构;也有较多类型的铸件的浇注位置在辅以砂芯或中箱或曲面分型等工艺措施后,亦可以实现其铸件设置于下型(或主要部分置于下型)。然而,在现实生产中有很多的铸件,尤其是以下几类典型结构的铸件,很多铸造厂仍经常采用将铸件分割置于上、下型的做法,甚或是铸件全部设置于上型的工艺方案。生产实践表明,这种方法较容易导致气孔、浇不足、缩孔、缩松、错边等铸造缺陷。
各类铸铁(钢)轮类铸件的砂型铸造,亦普遍采用的是一些常用手册或教科书上较为通常推荐的图2所示的上、下箱各置铸件一半铸件结构的浇注位置铸造工艺方案。
轮类铸件在铸造时容易出现缩孔、气孔、夹砂、裂纹和砂眼等铸造缺陷,或容易出现缩孔、裂纹、砂眼缺陷。轮类铸件的图2所示上、下箱各置一半铸件结构的传统铸造工艺方案,该种工艺方案(状态)在各类铸造厂都较为普遍存在,其气孔、缩孔等缺陷亦通常为该类铸件废品的主要因素。
给纤框图用图3(a)所示的上、下箱各置铸件一半结构的浇注位置的传统铸造工艺方案,在实际铸造生产中铸件易在冒口颈处产生缩孔缺陷。而核电行星架球墨铸铁件用图3(b)所示的上、中、下箱根据铸件结构各置一部分铸件结构的铸造工艺方案,该工艺方案在西南某厂采用的铸造生产方式是:水玻璃砂造型、制芯(铬铁矿砂制作特异小砂芯),一箱一件,大量设置冷铁,阶梯进液的浇注生产方式;加之其原始铸造工艺方案未设置适宜大的排气冒口,铸件在其浇注位置的顶面产生较多较大的气孔缺陷,且在顶面6个较大的热节处(A~F处)还间或产生缩孔缺陷。
为解决图3(a)所示给纤框的缩孔缺陷,一些铸造工作者往往采用加大冒口的工艺措施,而使得其铸件的缩孔缺陷变得更大。为解决图3(b)所示核电行星架大型球铁件的缩孔缺陷,传统的工艺措施是在顶面的6个热节处(A~F处)各设置一个大冒口(在图3b的原无冒口工艺方案的基础上改为其图示的大冒口工艺方案),而大冒口工艺方案进一步使得A~F 6个热节处(冒口颈)的缩孔缺陷更为严重。
铸件设置于下箱工艺方案的优点
分析图1至图4所示的几种典型铸件传统的铸造工艺方案,该几类铸件易产生或(间或)产生气孔、缩孔、缩松、错箱等铸造缺陷,笔者认为其共同的主要成因之一是:铸件的重要结构、或全部结构设置于上箱的浇注位置。
根据笔者30年来的铸造工厂生产实践经验总结和思考认为:铸件结构全部设置于下箱(铸件结构自然允许者)、或创造(工艺)条件将铸件全部结构或铸件重要结构设置于下箱,是解决众多黑色金属铸件砂型铸造易产生气孔、缩孔、缩松、错箱等铸造缺陷的最好浇注位置设计方案,亦即笔者极力主张“砂型铸造铸件下箱优先设置”,如图5至图8所示。铸件结构下箱优先设置方案,比之于图1至图4所示的铸件传统的浇注位置铸造工艺方案,主要具有如下几个方面的工艺优点。
图5至图8所示的铸件分型面设置方案,铸件结构全部设置于下箱、或创造工艺条件将铸件全部结构(或铸件重要结构设置于下箱)的浇注位置铸造方案,其极为重要的铸造工艺优点之一便是:充分地利用上、下箱的分型面对型腔进行排气,其分型面是一个天然(自然)的排气面,而且其处于铸件的最高面处(铸件结构自然允许其全部设置于下箱或创造工艺条件将铸件全部结构设置于下箱)或其处于铸件主要结构的最高面处(创造工艺条件将铸件重要结构设置于下箱)。
这种分型面处于铸件顶面或铸件主要结构面,利用分型面排气的方式是砂型铸造工艺中极为可靠、有效和充分的排气方式和途径,是解决相关黑色金属铸件砂型铸造气孔缺陷的重要工艺方法和技术措施。
图5至图8所示的铸件浇注位置及分型面设置方案,因铸件结构全部设置于下箱、及创造工艺条件将铸件全部结构或铸件重要结构设置于下箱,其为铸件浇注系统的优化设置创造了基础(工艺)条件,铸件可很好地设计出顶注式浇注(系统)方式。
顶注式浇注(系统)方式,因其能使金属液在型腔的温度梯度分布呈上高下低的正温度梯度状态,一方面十分有利于浇注系统及上层高温金属液对下层低温金属液的液态冷却收缩进行有效地补缩;另一方面,顶注式进液过程中、后进人型腔的金属液,可不断地使先进入型腔中的金属液的液面形成的“固态膜”破裂,从而极为有利于金属液中气体的溢出。
图5至图8所示的铸件浇注位置及分型面设置方案,因铸件结构全部设置于下箱、及创造工艺条件将铸件全部结构或铸件重要结构设置于下箱,也为铸件冒口系统的优化设计创造了基础(工艺)条件,铸件可很好地设计出压边冒口系统型式或其它类似于压边冒口之优化型式的顶冒口系统。
压边冒口系统型式(或其它优化型式的顶冒口系统),结合上述金属液在型腔中的温度梯度分布呈上高下低的正温度梯度状态,一方面十分有利于冒口系统对下层低温金属液的液态冷却收缩进行有效地补缩;另一方面,压边冒口系统型式因其在金属液自始至终充型的过程中处于铸件结构的最高处(或冒口因其在金属液自始至终充型的过程中处于铸件重要结构的最高处),极为有利于型腔中及金属液中气体的溢出。
铸件结构全部设置于下箱、及创造工艺条件将铸件全部结构或铸件重要结构设置于下箱,用图5至图8所示的铸件浇注位置及分型面设置方案,可较好地减小铸件的加工余量,减小(少)铸件飞刺。
减小铸件的加工余量,主要表现在以下几个方面:其一,铸件结构全部(或主要结构)设置于下型,只有下模一个方向的“拔模”斜度及错箱的可能性小,其铸件侧面的加工余量可适当减小;其二,因铸件的浇冒口设置于图5至图8所示的浇注位置的铸件顶面(即分型面或加工面),可以免去图1至图4所示铸件传统的铸造工艺方案在一些铸件的非加工面设置冒口而增加的“工艺”加工余量。
减小铸件飞刺,主要表现在铸件结构全部(或主要结构)设置于下型、其分型面在铸件顶面,可减少(小)50%左右分型面在铸件中部时传统的“防压环”结构,故而铸件用图5至图8所示的铸件浇注位置及分型面设置方案可比图1至图4所示传统的浇注位置铸造工艺方案至少减少40%~50%的铸造飞刺。
生产实践表明,铸件结构全部设置于下箱,即用图5至图8所示的铸件浇注位置及分型面设置方案比之于铸件用图1至图4所示传统的浇注位置铸造工艺方案铸造铸件,具有以下几个主要技术优点及经济效果:
(1)有利于克服气孔、缩孔、缩松、错箱等铸造缺陷的工艺优点,故其铸件的合格率高,尤其是可大幅度地提高气密性铸件的铸造合格率(可从常用铸造工艺方案的30%~40%提高到“铸件结构全部设置于下箱”工艺方案的95%左右);
(2)具有加工余量少,铸件的工艺出品率较高及砂箱面积利用率高的优点;
(3)获得内部组织更加致密、外形更加美观的高品质铸件。
免责声明:本文系网络转载,版权归原作者所有。如涉及作品版权问题,请与我们联系,我们将根据您提供的版权证明材料确认版权并于接到证明的一周内予以删除或做相关处理!
友情链接 友链交换添加QQ:2694467624 其他问题请咨询网站客服