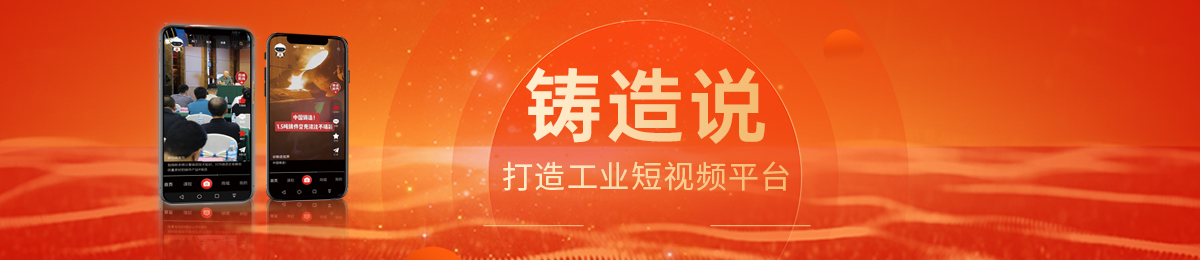
您好, 欢迎来到百铸网! 热线电话:400-8088-177 企业邮箱:[email protected] 注册|登录
2016-03-04来源:暂无数据
一、蜡料
蜡料是精铸生产中的第一个环节。众所周知, 由于铸件生产的发展, 相应地对蜡料的要求也是多种多样的。生产者最简便的方法是从市售的蜡料中选用,也可以自己配制,还可以委托专业工厂按要求生产。但无论何种蜡料其要求的性质是相同的, 即: 熔点、凝固点、软化点、导热性、流动性、收缩性、缩陷性、强度、硬度、韧性、离型性、涂挂性、回用性、尺寸稳定性及高温灼烧后的残留灰分量等。我们在具体铸件生产的基础上, 选用一种蜡料, 要求蜡料在某些方面具有的特点、有主有次;同时从成本上加以考虑也是重要因素。为了满足各种铸件的具体要求,蜡料分为液态、半液态、半固态、固态; 有填充料的和无填充料的;水溶性的和非水溶性的;再生的和非再生的; 蜡模用的、浇注系统用的、粘接用的、修补用的、密封用的, 树脂类蜡料等。单从蜡模用蜡料来说, 其品种也极多, 并且在继续发展中。有填充料的蜡料( FILLER WAX) 应用得比较广泛,常用的填充料是粉状聚乙烯、聚苯乙烯、有机酸、脂肪酸及淀粉等。其加入量为总量的30 %~45 % , 这类蜡料有很好的保温性, 即在较低温度下能成形, 其流动性好, 蜡模细部可清晰再现, 例如加有热硬性苯乙烯、加有异苯二甲酸及加有商品名为P2 FILLER 的三种蜡料, 从104 ℃降到49 ℃的时间各为59 秒、62 秒及99 秒, 这说明填充料的种类对蜡料性能的影响是较大的。这类蜡料的收缩率比无填充料的要小5 %以上。与蜡料性能密切相关的问题是蜡料的制备、使用及处理方法对蜡料性能的影响。
1、防止蜡料在熔化过程中过热
(1) 使用间接加热的油浴炉并使导热油强制循环, 熔化温度控制在84~98 ℃范围内, 并使其始终处于搅动状态, 目的除了使温度均匀以外, 对含填充料的蜡料还有防止沉淀的作用。过高的温度及局部过热均会因蜡料氧化、炭化等问题而使蜡料的性能变坏。过热的表现是蜡的颜色发生变化, 盛蜡桶内壁产生黑斑, 因填充料的分离而呈半透明状, 盛蜡桶内产生烟雾或蒸发物。
(2) 蜡在回用处理时, 为了去除杂质和水分, 必须加热到蜡的熔点以上, 通常控制在120 ℃以下, 在保证蜡料有一定的流动能力以去除杂质外, 其所含水分也会因搅拌器的搅动而得以蒸发。
(3) 对于在保温筒保温下使用的压蜡棒, 其加热温度只需比射出温度高2~3 ℃就可以了。
(4) 蜡料在高压釜(压力罐) 内脱除时, 蒸气温度可高达150 ℃以上, 这种条件是造成蜡料性能变坏的主要环节, 所以设法降低脱蜡温度、降低脱蜡压力以保持蜡料的性能。
2、保持环境温度
在蜡模制造室内, 无论是冬季或夏季, 室内温度都应保持在20~25 内, 使蜡模的尺寸处于一个稳定的环境中, 同时与沾浆制壳工序的环境条件相配合,以保证型壳的质量。
(1)、 蜡料的加热保温
蜡料在压力下从盛蜡桶进入压型, 在型中冷却凝固。在这一过程中, 温度差是影响蜡模的形状、尺寸及稳定性的主要因素。因此, 在用蜡桶保温蜡料而进行压蜡时, 蜡桶温度的均匀性是极为重要的, 同于蜡料的导热性差, 借助蜡桶的热量使蜡料均匀是困难的, 温度不均匀的蜡桶是生产不出健全的蜡模的。为此, 通常用保温槽对蜡桶进行加热保温, 保温槽通常可设定在58~62 ℃内, 略高于射出温度。在较长时间, 至少8 小时以上加热均匀化以后才能使用。保温槽是一个油浴加热装置, 导热油在油泵压力下循环流动, 使蜡桶在均匀温度下加热保温, 保温槽的温度控制器可按需要设定所要求的温度。温度不均匀的蜡桶在压蜡时, 蜡模会产生充不满、冷隔、粒状表面、流纹及网状纹等缺陷。
(2)、 蜡模的成形方法
根据铸件的大小、形状和技术要求产生不同的成形方法。而不同的成形方法又有不同的蜡料相配合。从压蜡的动力分, 有手动、电动、气动、液压等; 从压力分, 有低压、中压、高压等; 从蜡料状态分, 有液态、半液态、半固态、固态等; 从压型分, 有金属型、橡胶型、石膏型等, 从铸件分, 有工业品、艺术品等等。
二、压蜡成型机(压蜡机)
蜡料在压蜡机中被压成蜡模, 也就是蜡模的性质在很大程度上受压蜡机参数的制约, 这直接关系到压蜡机的设计、结构和性能。例如对一台直立式高压半固态压蜡机来说, 在进行压蜡操作以前, 必须先检查蜡料温度、射出压力、压射时间、冷却时间、压型温度。然后根据工艺卡的规定进行操作。压蜡成形机的性能主要表现在它所能调节的工艺参数, 其中包括, 手动式、自动式; 蜡桶温度调节、注蜡口温度调节; 合型力调节、合型行程调节; 压射压力调节、压射速度调节、压射时间调节; 回程速度调节等。例如有的铸件, 其蜡模两端各有两个孔环,由于孔环与本体的连接比较薄弱, 所以在连接处易发生肉眼可见的微裂纹, 后来通过调节射出速度和保持时间, 这种缺陷就消除了。由此可知, 压蜡机所能调节的工艺参数及其调节范围、调节方法及正确控制对制造合格蜡模是极为重要的。压蜡机的中心部分是蜡筒。其尺寸为<100mm ×400mm , 用来放置蜡棒, 经充分预热的蜡棒放入蜡筒中, 而蜡筒用电加热, 温度保持在射出温度上, 当压型的注入口放到蜡筒的注蜡口(射出口) 后(注蜡口有独立的加热保温系统) , 即可启动油泵, 驱使上部活塞向下移动, 把蜡料压入型中; 保压一定时间后, 折开压型, 取出蜡模。全过程的主要参数是: ①半固态蜡料的温度控制在稍高于射出温度, 通常取55~60 ℃, 为使蜡筒温度均匀, 表里一致, 蜡筒必须在保温槽内停留8 小时以上; ②射出压力是可调节的, 通常为214~218MPa ③压蜡机给压型的紧固力是可调的, 通常为310~315MPa ④射出速度是用射出时间来实施的, 它因蜡模形状不同而不同, 它与蜡模收缩情况有很大关系, 从而影响蜡模质量。
三、蜡模缺陷
由于种种原因, 压蜡成形机所制造的蜡模会产生 一些缺陷, 主要有下列几种: 1、充不满
主要原因是蜡料的温度较低, 射出速度慢、压型温度较低, 造成蜡料在流动过程中冷却快, 表现在角和边的部分或蜡模的薄壁部分充不满, 棱角的地方出现圆角, 与金属铸件的浇不足相似。
2、气泡
一种是表面气泡, 即用肉眼可见的皮下气泡, 有个别分布, 有密集分布; 另一种是蜡模深层的气泡,通常是集中性的较大的气泡, 肉眼无法看到, 但从蜡模的局部鼓起, 出现于蜡模的中心部分和最后冷却的部分, 这是内压力的释放, 气体膨胀的结果。
3、表面皱纹
由于蜡料温度不够, 压射速度较低, 蜡料运动与压型温度的配合不当; 或由于压型内表面受损或不清洁; 激冷金属块放置不当等, 在蜡模表面留下运动的痕迹。纹路较深的, 类似金属铸件的冷隔缺陷; 轻微的皱纹可以打磨除去。还有就是在型芯周围、孔洞的周围, 有时可见到接缝, 略呈凹陷, 实际是二股蜡流的会合处未能很好熔合, 这是蜡料的温度不够、压力不足的结果。
4、表面粗糙
由于射出压力过小、或射出速度不够, 蜡料与压型内表面的接触密度不够, 不能如实地反映压型的表面状态, 严重的还伴有皱纹。
5、缩凹
蜡模表面凹陷, 主要是射出压力及时间不够, 或是蜡料温度较高, 冷却时间不够有时离型脱模剂太多, 也可能使蜡料性质下降。表面缩凹涉及较大面积, 修理比较困难。
6、变形
蜡模从压型中取出后, 除了尺寸发生缩小变化外, 因取出时手法不妥而人为造成变形; 由于蜡模仍在冷却而使温度场发生变化而挠曲变形是常见的。所以刚从压型中取出的蜡模仍要小心安放, 通常以较大平面为基准放平, 必要时使用与变形部位相适应的形状, 做成金属块嵌入蜡模防止变形, 也即使其充分冷却。也可能蜡料太软, 压型的组成部件不合适等。
7、毛翅(披缝)
这是最常见的一种缺陷, 即在压型合型处, 压型组合块的接合处, 型芯与芯座的连接处等地方有很薄的蜡片逸出。其产生的原因主要是压型精度不够, 压型分型面或型内部件接合面受到损伤或附着不洁物,或合型力不够, 射出压力过高。或者蜡的温度过高。毛翅必须彻底清除掉, 蜡模才能使用。
8、粘着
蜡模与压型粘着是因为没有使用离型剂, 或是蜡与压型的温度均太高, 或是压型受损害、压型不清洁所造成。
四、结语
蜡模制造与随后的组装、制壳、脱蜡、浇注、清整一样, 要强调的是操作工艺的重要性, 各个环节之间的配合, 必须执行各个工序的工艺卡及相关的技术管理文件。并要在贯彻执行中不断完善有关文件以适应正常生产的需要。每个岗位上的工作人员必须对有关的工艺卡中的内容和要求有充分的理解和切实的执行, 否则尽管有各类技术文件, 其结果形同虚设。在缺陷的防止、材料利用、设备维修, 工夹具制造和检验、废品分析、修补、报废等方面都要有章可循, 有人负责, 将工艺制度切实地贯彻在整个生产活动中。
友情链接 友链交换添加QQ:2694467624 其他问题请咨询网站客服