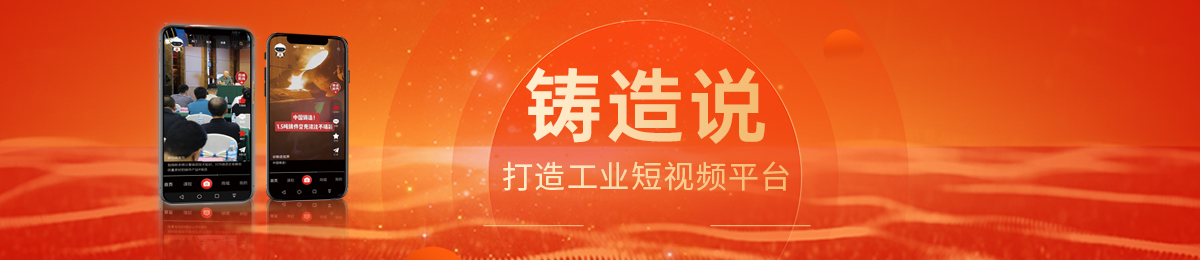
您好, 欢迎来到百铸网! 热线电话:400-8088-177 企业邮箱:[email protected] 注册|登录
2016-07-14来源:暂无数据
1.概述
众所周知,车桥是车辆的重要承载零件,它直接关系到车辆使用的安全性。而桥壳是车桥的关键零部件之一,桥壳材料性能的好坏,直接决定了车辆的承载能力。目前,重卡行业的桥壳一般分为冲焊桥壳和铸造桥壳两大类,并且铸造桥壳又可分为铸钢桥壳和铸铁桥壳。
铸造桥壳以其承载重量大,生产成本低的特点一直占据着重卡桥壳的主要地位。因桥壳的工作环境恶劣,长期在动载荷状态下工作,这就要求桥壳的材料性能有很高要求,在保证强度的同时,还需要得到更高的塑性和韧性,来适应桥壳的工作特点。
我们知道,对于球墨铸铁来说,球化处理工艺是球墨铸铁生产的关键环节,球化处理效果的好坏直接影响到球墨铸铁的质量。起初,我们采用的球化处理工艺是冲入法球化处理,此种方法虽然简单,易操作,但是还有许多不足之处,如:合金收得率低;烟雾大,工作环境差;反应时产生的渣量多;处理效果易受到外部因素影响,导致铸件质量出现波动,经常出现球化不合格现象。这些质量波动会导致桥壳的性能受到影响,甚至影响到车辆的安全性。
喂线法球化处理工艺应用于铸铁生产,国外始于20世纪80年代,而国内球墨铸铁的生产对于该技术的应用起步虽然较晚,但该技术在国内的推广使用快,且对于提高球墨铸铁质量的稳定性效果明显。为进一步改善球铁桥壳的质量,提高其性能,我们引进喂线球化法来提高桥壳的球化质量(见图1)。
图1喂线球化处理
2.喂线球化处理工艺
喂线球化处理工艺的基本原理就是将一定成分的粉状球化剂和孕育剂通过钢皮包裹,通过设备以一定速度送入到球化处理包中,使其在包底球化起爆,达到球化孕育处理目的。
目前,我们采用的喂线球化处理工艺为:调整化学成分至工艺要求,升温至1510~1520℃静置,出炉温度1480~1500℃,出铁量2t,球化处理温度1420~1450℃,浇注温度1370~1380℃。随流孕育量0.1%。
加入球化线长度39~46m,根据原铁水硫含量进行调整,硫含量越高,需要加入的球化线越长,反之亦然。孕育线长度为32m。
3.喂线球化工艺对铸件质量的提升
经过一年多的生产,我们的桥壳质量相对于以前有了明显提升。特别是成分、金相、力学性能的稳定性有了很大提高。
(1)主要成分对比 我们随机抽取了冲入法和喂线法工艺各50个班次的铁液成分数据,其中每个班次抽取10组数据,分析结果见表1。
4.喂线球化工艺的优点
根据我们实际生产对比,喂线球化处理工艺相对于冲入法球化处理工艺有很多优势。
(1)现场生产环境的改善 冲入法球化时,因球化剂与铁液反应,产生大量烟雾和强光,使现场工作环境变得恶劣;喂线法球化时,因其处理站中有包盖可以盖住球化包,同时包盖与处理站的除尘系统相连,使烟雾通过除尘系统处理掉,而不是直接释放在车间里。
(2)合金加入量减少,降低生产成本 经过计算,处理1t铁液喂线法比冲入法可节约原材料成本约78元,按我厂年产1万t球墨铸铁桥壳产能计算,年节约成本78万元,效益可观。
(3)实现作业自动化,降低工人的劳动强度 冲入法球化处理时,工人的前期准备工作繁琐,包括球化剂和孕育剂的称量,向包内加入球化剂和孕育剂,并且需要捣实和覆盖操作;喂线法的球化线和孕育线的加入量通过控制柜控制自动加入,减少了大量工作。
(4)球化质量稳定,球化效果更好 经统计,自2013年使用喂线球化处理工艺后,球化合格率为99.5%以上,而冲入法球化处理的合格率仅为95%。
5.如何正确选择喂线球化工艺参数
在实际生产中,如何正确选择喂线球化工艺的参数,需要一定次数试验的验证。我们自开始组织试验到正式批量生产,期间经过了多次的工艺调整。下面将把我们的使用经验与同行分享。
要正确选择喂线球化的工艺参数,需要注意以下几个方面:
(1)包芯线的选择 国外一些经验不建议选用高Mg含量的包芯线,Mg含量过高,球化反应剧烈,Mg的烧损多,渣量大。一般建议选用Mg含量为30%左右,并选用含Ba孕育线,能有效防止孕育衰退。我公司使用的包芯线的主要参数为:外包钢皮厚度0.4mm,芯线直径为13mm。使用前应注意检查包芯线外观应圆整,无裂痕、漏粉等。
6.结论
(1)喂线法球化工艺合金加入量低,Mg吸收率高,且能有效减少车间的烟雾和强光污染,为铸造企业创造良好的经济和环境效益。
(2)喂线法球化工艺能有效减少球化不合格率,提高球墨铸铁的质量,提高其综合力学性能,增强企业的市场竞争力。
(3)各个铸造厂要根据自身生产条件及产品的工艺要求,结合同行的生产经验,来选择合适的喂线球化工艺参数。
结语
喂线球化工艺可以显著提高球墨铸铁质量的稳定性,降低生产成本,改善生产环境,降低工人劳动强度,是最近球化处理工艺的发展趋势。
友情链接 友链交换添加QQ:2694467624 其他问题请咨询网站客服