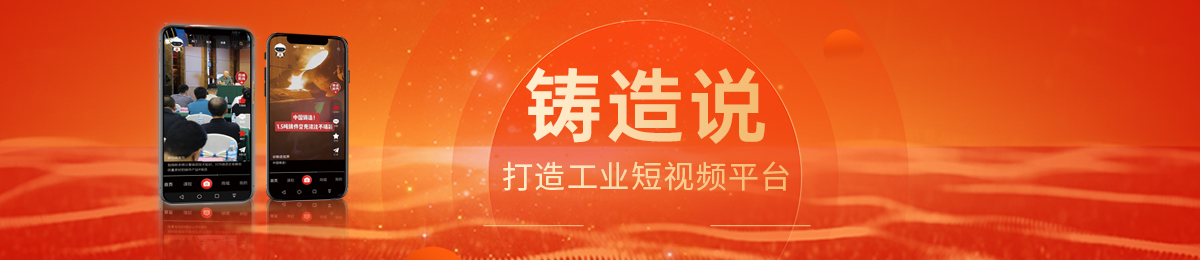
您好, 欢迎来到百铸网! 热线电话:400-8088-177 企业邮箱:[email protected] 注册|登录
2016-07-11来源:暂无数据
图1 单件重达635 kg铝合金线圈支座壳体铸件
艾克的项目主管工程师丹霍弗特(Dan Hoefert)说。“如果要获得健全的铸件,不得不对设计进行一些修改。我们通过模拟软件优化了这个零件,对浇冒口进行了7、8次迭代模拟。”
客户强调了这个直径1.5米,高1.14米的铸件内部质量健全的重要性。当工程师最终完成了设计的时候,艾克公司研究了尽量降低这个单件铸件模具费用的问题。工艺设计包括选择分型面,尽可能降低拔模斜度。还有,需要采用14个芯子以实现复杂的几何形状(图2)。艾克公司选择采用高密度泡沫材料制作模具,这可以为客户节省10多万美元费用。
图2 壳体铸件的14个芯子采用高密度泡沫材料芯盒制作
采用多个冷铁以使铸件凝固均衡,并且降低半脆性的高密度泡沫模具的应力。采用内补缩冒口以保证铸件内环圈无缩松、缩孔缺陷,内冒口在随后的机加工过程中去除。当设计完成,模具制备好了以后,艾克公司开始准备熔炼862 kg铝合金熔液生产这个重635 kg的铸件。
“我们相信我们的工程师,相信我们对这个复杂铸件的模拟能力,”霍弗特说。“但是,你还是不得不期待着好的结果,因为在生产过程某一点上你是控制不了的。”
等这个大型铸件浇铸完成,冷却之后,去除浇冒口然后进行热处理。铸件通过着色渗透探伤检验合格之后,送往第3方进行机加工,最终在限定的紧迫时间期限内交付给客户。
“客户告诉我们他们对铸件非常满意,”霍弗特说。“生产像这样的单件铸件是极具挑战性的,因为要第一次就浇铸成功,有太多的工作要做。”
友情链接 友链交换添加QQ:2694467624 其他问题请咨询网站客服