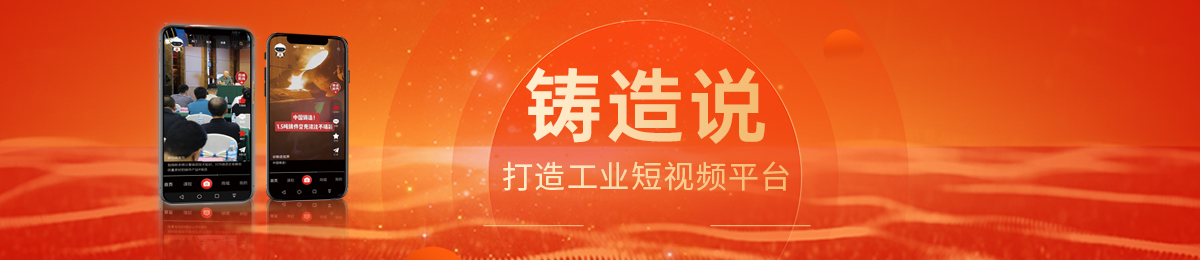
您好, 欢迎来到百铸网! 热线电话:400-8088-177 企业邮箱:[email protected] 注册|登录
2016-06-29来源:暂无数据
上世纪60年代后期,晶闸管静态变频电源的应用,导致铸铁行业中采用无芯感应电炉作为熔炼设备的企业逐渐增多,尤其是70年代逆变电源的开发,中频无心感应电炉的电源有了重大的改进,频率转变效率可提高到97%~98%,熔化铸铁时热效率可达到70%,同时,电炉设备和所用的耐火材料也在不断发展,因而其应用日益广泛。
对于不适于采用长炉龄大型冲天炉的中、小型铸铁企业,用无心感应电炉熔炼有很多优点,主要如:
l 熔炼时排出的废气、烟尘和炉渣大幅度减少,便于治理环境和改善作业条件;
l 可利用廉价的金属炉料,尤其是便于循环回用加工的切屑和边角余料;
l 生产安排的灵活性较好;
l 铸铁的化学成分和温度比较均匀且易于控制。
但是,感应电炉熔炼的冶金过程与冲天炉有很大的的差别,如果不能切实了解其冶金特点,从而正确安排熔炼和各项后处理作业,则生产灰铸铁件时,往往会出现显微组织不符合要求、铸件的加工性能恶化等各种问题,不能确保铸件的质量要求。
一、感应电炉与冲天炉熔炼过程中的不同之处
冲天炉是以焦炭为燃料的竖炉,无芯感应电炉则是以电感应加热的坩埚炉,熔炼过程当然会有很大的的差别,即使熔炼得到的铁液化学成分相近,其在凝固过程中发生共晶转变的条件却有很大的差异,因而,铸件的微观组织和某些性能也会有颇大的差异。
这两种熔炼设备,不同之处主要有以下几点。
1、冲天炉内有高温的过热区
冲天炉熔炼过程中,在底焦层内氧化带和还原带之间,有一高温过热区,温度一般都在1700℃左右,高温运行的冲天炉还会更高一些。
感应电炉熔炼时,炉内不存在这样的过热区。
2、铁液中的硫含量
冲天炉熔炼时,炉料中生铁锭所占的配比较高,生铁锭的硫含量一般都高于废钢。而且,炉料在熔化区熔融后,以细小液滴状态下落的过程中,流经硫含量较高的焦炭,二者接触的界面面积大。液滴到达炉缸后,所有的铁液都积存于焦炭块之间的空隙中。因此,熔炼灰铸铁时,铁液中的硫含量较高,通常都在0.1%左右。
无芯感应电炉熔炼铸铁时,由于炉料中废钢多而生铁锭少,配料中硫含量本来就低,再加以熔炼过程中完全不与焦炭接触,没有自焦炭吸收硫的过程,如果不特意在配料中加硫,则熔炼得到的铁液中硫含量较低,一般都在0.04%以下。
3、铁液中的氧含量
冲天炉熔炼过程中,未熔的金属炉料、铁液与炉气接触的界面大、时间长,熔炼制得的铁液中氧含量较高,一般为0.004%~0.006%。
无芯感应电炉熔炼铸铁时,金属炉料与炉气接触的时间很短,熔融的铁液与炉气接触的界面很小,铁液中的氧含量相当低,一般为0.002%左右,甚至更低一些。
高炉熔炼的铸造生铁,氧含量比废钢高得多。少用或不用生铁,代之以废钢,也是感应电炉熔炼的铁液中氧含量较低的重要原因。
4、铁液中的氮含量
冲天炉熔炼过程中,虽然铁液与炉气接触的时间长,接触的界面大,但是,由于铸铁中的碳、硅含量较高,溶于铁液中的氮并不很多,含量一般为0.004%~0.007%。铸铁中含有少量的氮,铸件中不至于产生气孔,却有促成珠光体的作用,有助于改善铸铁的力学性能。
无芯感应电炉熔炼铸铁时,炉料中配用的废钢量较多。废钢中的碳、硅含量都低,氮含量比铸铁中的高得多,因此,感应电炉熔炼的铁液中氮含量要高一些。一般说来,炉料中废钢用量为15%时,铸铁中的氮含量约为0.003%~0.005%;废钢用量为50%时,氮含量可达0.008%~0.012%;炉料全部为废钢时,氮含量可高达0.014%以上。
如果铁液中氮含量在0.01%以上,铸件就易于因氮析出而产生气孔。因此,用感应电炉熔炼时,要注意防止因氮而致的气孔。
5、对铁液的搅拌作用
冲天炉熔炼过程中,炉料熔化后,只在液滴下落的短暂时间内有些扰动。铁液进入炉缸或前炉后,除内部有轻微的对流外,基本上没有搅拌作用。
感应电炉熔炼过程中,熔融的铁液内部自始至终都有感应电流的搅拌作用。
二、感应电炉熔炼制得的铁液共晶结晶时的过冷度大
在碳当量相同的条件下,用感应电炉熔炼的铸铁与用冲天炉熔炼的相比,共晶结晶时的过冷度大得多,参见图1。
碳当量[C+1/3(Si+P)] (%)
图1 在不同的碳当量下铸铁的熔炼条件对共晶结晶时过冷度的影响
a-冲天炉熔炼;b-感应电炉熔炼
在碳、硅含量相同的条件下,用感应电炉熔炼的铸铁与用冲天炉熔炼的相比,三角试片的白口宽度也有明显的差别,参见图2。
铸铁的碳含量(%)
a1-冲天炉熔炼,Si2.5%;a2-冲天炉熔炼,Si 2.0%;
a3-冲天炉熔炼,Si 1.5%;b1-感应电炉熔炼,Si2.5%;
b2-感应电炉熔炼,Si 2.0%;b3-感应电炉熔炼,Si1.5%
图2 用不同熔炼条件熔炼的铸铁碳、硅含量对三角试片白口宽度的影响
由图1、图2可见,熔炼条件不同的铸铁,共晶结晶时特性差别很大。感应电炉熔炼制得的铁液,过冷度大,其原因主要有以下三个方面。
1、共晶结晶时晶核的数量减少
冲天炉熔炼时,从炉料开始熔化到铁液自炉中流出所经历的时间很短,大约是10min左右。感应电炉熔炼时,从炉料开始熔化到出铁一般要经1小时左右,而且又有感应加热所特有的搅拌作用,易于使铁液中微细的碳质晶核溶于铁液。与此同时,可在共晶结晶时作为异质晶核的微细颗粒也大幅度减少。例如,可作为异质晶核的SiO2,在温度很高、又有搅拌作用的条件下,易于与铸铁中的碳发生如下反应而生成硅,硅溶于铁液,异质晶核消失:
SiO2+2C→Si+2CO↑
因此,用感应电炉熔炼灰铸铁时,要特别注意做好孕育处理作业,孕育剂用量应比冲天炉熔炼时略多一些,最好出炉前先在炉中进行预处理,以改善铸铁共晶结晶时的生核条件。
2、铁液中的硫含量低
前面已经谈到,用感应电炉熔炼铸铁时,熔炼得到的铁液,硫含量一般都在0.04%以下。可是,对于灰铸铁而言,一定的硫含量是保证微观组织正常所不可或缺的。
浇注前向铁液中加入孕育剂后,孕育剂中的活性元素与铁液中含有的硫、氧作用,生成大量微细的氧化物、硫化物和硫氧复合化合物,弥散于铁液中。在灰铸铁铁液的共晶凝固过程中,这些细小的夹杂物能作为石墨析出的异质晶核,促进石墨生核、使共晶团数量增多、共晶团细化。
因此,用感应电炉熔炼时,应特别关注铁液中的硫含量,必须使之保持在0.06~0.08%之间。如配料中没有引入硫的组分,一般可加入适量的硫化亚铁使之增硫。
感应电炉中加入硫化亚铁的量很小,硫含量往往不易准确控制。最近,日本有人提出,应该在为生产高档灰铸铁件而提供的高纯生铁中,特意配加一定的硫含量,以便于铸造厂的质量控制。
3、铁液中的氧含量低
前面已经谈到,用感应电炉熔炼的铸铁中,氧含量一般都较低。如果氧含量降低到0.001%以下,铁液中可以作为外来晶核的氧化物、硫氧复合化合物就很少,铁液对孕育处理的回应能力就会很差。对于灰铸铁而言,作为异质晶核,氧化物尤为重要。
在确认铸铁中氧含量过低的情况下,就应适当增加氧含量。最方便的办法是采用含氧、硫的孕育剂。这种孕育剂,国外早已有供应,随着我国用感应电炉熔炼的铸铁企业日益增多,近来也已经有有类似的产品问世。
在炉料中配入30%左右的铸铁切屑,既可以循环利用废弃物料、降低生产成本,又可以使熔炼制得的铁液中氧含量增多,不失为一种可取的增氧措施。美国某铸铁厂,炉料中铸铁切屑的用量为50%。
三、炉料中生铁块太多会导致石墨组织异常
前面曾经提到,用感应电炉熔炼铸铁时,由于液态铸铁在炉内保持的时间长,又有感应电流的搅拌作用,会使微细的碳质晶核溶于铁液,同时,能作为外来晶核的氧化物、硫化物和硫氧复合化合物也会大量损失。但是,对于生铁锭中所含的粗大石墨,情况就不一样了。
生铁锭中,一般都含有粗大的片状石墨。冲天炉熔炼时,即使出铁的温度不太高,炉内过热区的温度也在1700℃左右。铁液通过过热区所经历的时间虽然很短,但却是以细小液滴通过的,能得到高温过热,有助于使石墨溶于铁液。因此,即使炉料中配加的生铁锭较多,只要铸铁的成分不是过共晶的,显微组织中的石墨都呈细小的片状,一般不会有块片状(C型)石墨出现。
感应电炉熔炼铸铁时,虽然液态铸铁在炉内保持的时间长,又有感应电流的搅拌作用,但炉内的温度毕竟比冲天炉熔化带的温度低得多。如果炉料中配用的生铁锭太多,就不可能使熔点高、稳定性强的片状石墨全部溶入铁液,总有一些晶态石墨保留在铁液中。
在这种条件下,铸铁开始凝固前就存在较大的晶态石墨,即使铸铁的成分是亚共晶的,凝固时也会有初生石墨依托晶态石墨析出。最后,铸铁的显微组织中就会出现块片状(C型)石墨,影响铸铁的力学性能。
因此,用感应电炉熔炼铸铁时,炉料中生铁锭的用量最好不超过10%,以保证显微组织正常。
1980年,我曾在美国造访过7、8家用感应电炉熔炼、生产高档次灰铸铁件的铸造厂,二十多年前,就没有见到一家用一块生铁锭的。欧洲用感应电炉熔炼铸铁的铸造厂,炉料中生铁锭的配用量一般都不超过10%。
目前,我国还有不少铸造厂,将冲天炉熔炼时所用的炉料配比,原封不动地用于感应电炉,不少企业生铁锭的用量为30%,有的企业甚至高达50%。再加以未能按感应电炉的冶金特点安排适当的孕育处理,结果,显微组织中既有块片状(C型)石墨,又有D型、E型石墨(过冷石墨),这种不正常的组织当然有损于铸件的质量,希望能尽早纠正这种不合适的做法。
四、认真做好孕育处理和预处理
感应电炉熔炼的铁液,共晶结晶时的过冷度大,用以生产灰铸铁件,必须认真做好出铁时的一次孕育处理和浇注过程中的二次孕育处理。在此基础上,生产高质量铸件时,出铁前还应该在炉内进行预处理(preconditioning)。大批量生产高质量铸件时,还有必要考虑采用动态孕育工艺,以确保铸件质量的可重复性。
关于常规的孕育处理,有关的参考资料很多,不必在此处重复。这里,只想简要地介绍一下预处理和动态孕育工艺。
1、预处理
铸铁的预处理工艺,大约在上世纪70年代后期开始应用于欧洲,随后,差不多与感应电炉熔炼铸铁的工艺同步发展。1980年,笔者在美国造访了好几家用感应电炉熔炼铸铁的铸造厂,没有一家不采用预处理工艺,所用的处理剂都是碳化硅。目前,一些工业国家中,预处理工艺的应用面很广,而且已自感应电炉熔炼推广到冲天炉熔炼。
据笔者所知,目前美国用作预处理剂的碳化硅约70%自中国进口,而我国采用预处理工艺的铸造厂却很少很少。
预处理的作用不仅在于减轻激冷倾向和减少碳化物的形成,还在于改善共晶转变时石墨的生核和长大。出于对灰铸铁的冶金要求,希望在较高的温度下发生共晶转变、析出石墨,并使过冷度最小,从而保证得到A型石墨,防止产生B型、D型和E型石墨。而且希望发生共晶转变时石墨生核程度高,共晶团数量多,以得到细小的片状石墨。
通过预处理,生产薄壁铸件时,不仅可避免组织中出现碳化物,而且可使过冷型石墨(B型和D型)减至最少。预处理工艺可用于砂型铸造,也可用于金属型铸造和离心铸造。
铸铁所用的预处理剂,应该是含碳、硅的晶态材料,碳化硅的应用较广。对于灰铸铁,一般都采用SiC含量为85~90%的冶金碳化硅;对于球墨铸铁则宜采用SiC含量为97~98%的碳化硅。
人造石墨(晶态石墨)也可用作预处理剂。
75%的硅铁则只有提高硅含量的作用,作为预处理剂的效果不明显。
用碳化硅作预处理剂时,加入量一般为0.7~1.0%,实际应用时,应通过试验求得最佳值。
2、动态孕育工艺
铸铁是非常复杂的铸造合金,其显微组织和性能决定于很多因素,如:所用炉料的状况、炉料熔化的过程及温度控制、奥氏体和石墨在铁液中生核的条件、化学成分、所用的孕育方法、孕育剂的品种及其用量等。虽然生产和应用铸铁件已有两千多年的历史,大家对铸铁的结晶、凝固过程(奥氏体和石墨的析出和长大)一般也都有所了解,但是,时至今日,我们的认识仍然很不全面。而且,在生产条件下进行孕育处理时,对于孕育剂品种的选用、加入量的确定,所依据的资料和信息往往都是不够充分的,只能依据经验或过去的试验结果。因此,即使是很有经验的技术人员,也经常会遇到始料未及的问题。
(1)化学成分分析
现在,一般的铸造厂都配备有炉前快速分析的设施,很多铸造厂还配备了光谱分析仪,这对于控制铸铁的化学成分当然是十分必要的,但对于有效地控制铸铁的微观组织和性能则是不充分的。而且,用感应电炉熔炼的铸造厂尤其需要知道铁液中的氧含量。
实际上,炉前快速分析所能测定的元素是非常有限的,一些对铸铁组织有重要影响的微量元素都不能测定。采用光谱仪,能测定的元素多了,但对铁水中所含的气体、各种氧化物、硫化物、硅酸盐的含量以及其他影响铸铁凝固过程的因素,仍然无从知晓。
总之,炉前化学分析是必要的,但对于实施有效的工艺过程控制则是不充分的。因此,不同铸造厂生产的化学成分相近的铸铁件,性能可能有很大的差别。即使同一铸造厂,在不同时间生产的化学成分相近的铸铁件,其性能也不尽相同。
(2)热分析
要对铸铁的微观组织和性能进行有效的控制,除化学成分外,还必须依靠由热分析得到的数据和信息。
铸铁企业所用的热分析系统,目前大多都在试验样杯中加碲,使铸铁试样按亚稳定系凝固。通过这样的热分析,可以得知铸铁的液相线温度和按亚稳定系凝固时的共晶转变温度,并可由此推算碳、硅含量和碳当量。但对于生产灰铸铁、球墨铸铁和蠕墨铸铁件,都不能提供任何有关石墨化的信息。
因此,铸铁所用的热分析系统,应采用不加碲的样杯,使试样按稳定系凝固,并得到相应的冷却曲线。然后再由人工智能系统根据每一铸造厂设定的条件,就每一种合金解读其冷却曲线,并提供相关的信息。这种热分析系统可适应各企业的具体条件,通常称之为“自适应热分析系统”,简称“ATAS”。
最近开发的、控制蠕墨铸铁质量的NovaCast系统和SinterCast系统都是自适应热分析系统的发展。
(3)铸铁的动态孕育处理
动态孕育处理的特点是:孕育剂的加入量不是固定不变的,孕育剂的品种也不限于一种。进行处理时,根据成分分析和热分析得到的数据,实时地调整孕育剂的品种及其加入量,使铸铁的微观组织达到最佳状态。德国的铸造工艺研究所多年前就已就此编制相应的软件。这样,就可以有效地控制铸件的微观组织和性能,保持铸件的质量稳定、一致,防止铸造缺陷的产生,并使废品率降到最低水平。
五、增碳剂及其应用
冲天炉熔炼铸铁时,熔融的铸铁以液滴通过灼热的底焦,增碳效果很好,通常可以通过调整底焦高度、控制炉料配比和铁液温度来控制增碳量,有必要采用增碳剂的情况很少。
感应电炉熔炼铸铁时,炉内没有碳源,炉料中生铁锭的用量少、废钢的用量多,增碳剂一般都是必不可少的。增碳剂的品种及其特征,不仅影响增碳效率,对铸件的冶金质量也有重要的影响。
1、增碳剂
可以用作铸铁增碳剂的材料很多,常用的有人造石墨、煅烧石油焦、天然石墨、焦炭、无烟煤以及用这类材料组配成的混合料。
(1)人造石墨
上述各种增碳剂中,品质最好的是人造石墨(也有人称之为晶态石墨)。炉料中配加人造石墨,其作用不仅在于增碳,而且还有预处理铁液的效果。
制造人造石墨的主要原料是粉状的优质煅烧石油焦,在其中加沥青作为粘结剂,再加入少量其他辅料。各种原材料配合好以后,将其压制成形,然后在2500℃~3000℃、非氧化性气氛中处理,使之石墨化。经高温处理后,灰分、硫、气体含量都大幅度减少。
由于人造石墨制品的价格高,铸造厂常用的人造石墨增碳剂大都是制造石墨电极或其他成形部件时的切屑、废旧电极和石墨块等循环利用的材料,以降低生产成本。
熔炼冶金质量较高球墨铸铁时,增碳剂宜首选人造石墨,为此,最好向附近用电弧炉炼钢的企业或电解铝生产企业购买废电极,自行破碎到要求的粒度。
(2)石油焦
石油焦是目前广泛应用的增碳剂。
石油焦是精炼原油得到的副产品。原油经常压蒸馏或减压蒸馏得到的渣油及石油沥青,都可以作为制造石油焦的原料,再经焦化后就得到生石油焦。原油加工过程中,产出的生石油焦一般不到原油的5%。美国生石油焦的年产量约3000万吨。生石油焦中的杂质含量高,不能直接用作增碳剂,必须先经过煅烧处理。
生石油焦有海绵状、针状、粒状和流态等品种。
海绵状石油焦是用延迟焦化法制得的,由于其中硫和金属含量较高,通常用作煅烧时的燃料,也可作为煅烧石油焦的原料。经煅烧的海绵焦,主要用于制铝业和用作增碳剂。
针状石油焦,是用芳香烃的含量高、杂质含量低的原料,由延迟焦化法制得的。这种焦炭具有易于破裂的针状结构,有时称之为石墨焦,煅烧后主要用于制造石墨电极。
粒状石油焦呈硬质颗粒状,是用硫和沥青烯含量高的原料,用延迟焦化法制得的,主要用作燃料。
流态石油焦,是在流态床内用连续焦化法制得的,呈细小颗粒状,结构无方向性,硫含量高、挥发分低。
石油焦的煅烧,是为了脱除硫、水分和挥发分。将生石油焦于1200~1350℃煅烧,可以使其成为基本上纯净的碳。
煅烧石油焦的最大用户是制铝业,70%用以制造使铝矾土还原的阳极。美国生产的煅烧石油焦,用于铸铁增碳剂的约占6%。
各种石油焦制品的大致成分列于表1,供参考。
表1 各种石油焦制品的大致成分(%)
品 种 |
固定碳 |
硫 |
灰分 |
挥发分 |
水分 |
生石油焦 |
85~89 |
1~6 |
0.2~0.5 |
10~14 |
8~10 |
煅烧石油焦 |
98.5 |
0.02~3.0 |
0.2~0.5 |
0.3~0.5 |
≤0.5 |
合成碳制品 |
99 |
0.01~0.03 |
0.1~0.5 |
- |
≤0.5 |
低硫合成碳制品 |
99.9 |
0.01~0.03 |
0.01~0.03 |
- |
≤0.2 |
(3)天然石墨
天然石墨可分为鳞片石墨和微晶石墨两类。
微晶石墨的灰分含量高,一般不用作铸铁的增碳剂。
鳞片石墨有很多品种:高碳鳞片石墨需用化学方法萃取,或加热到高温使其中的氧化物分解、挥发,这种鳞片石墨产量不多、价格高,一般也不用作增碳剂;低碳鳞片石墨中的灰分含量高,不宜用作增碳剂;用作增碳剂的主要是中碳鳞片石墨,但实际用量也不多。
天然石墨的大致成分见表2。
表2 天然石墨的大致成分(%)
品 种 |
固定碳 |
硫 |
灰分 |
挥发份 |
水分 |
中碳鳞片石墨 |
85~95 |
0.1~0.7 |
5~15 |
1~2 |
- |
微晶石墨 |
60~80 |
0.1~0.2 |
20~40 |
1~2 |
0.5 |
(4)焦炭和无烟煤
电弧炉炼钢过程中,可以在装料时配加焦炭或无烟煤作为增碳剂。由于其灰分和挥发分含量较高,感应电炉熔炼铸铁时很少用作增碳剂。
关于铸造行业常用的几种增碳剂的成分和堆密度,表3中列出了一些典型的测定数据,可供参照。
表3 常用增碳剂的成分和堆密度
增碳剂 |
碳含量 (%) |
灰 分 (%) |
水分 (%) |
挥发分 (%) |
硫 (%) |
氮 (%) |
氢 (%) |
堆密度的概略值 (g/cm3) |
人造石墨 |
99.2 |
0.4 |
0.20 |
0.10 |
0.05 |
0.005 |
- |
0.84 |
鳞片石墨(中碳) |
85.3 |
13.2 |
0.06 |
0.44 |
0.35 |
0.060 |
- |
- |
煅烧石油焦(中硫) |
96.5 |
0.4 |
0.40 |
0.30 |
1.50 |
0.600 |
0.15 |
0.77 |
煅烧石油焦(低硫) |
98.3 |
0.4 |
0.10 |
0.20 |
0.30 |
0.080 |
0.04 |
0.800 |
干燥焦炭 |
87.7 |
9.0 |
0.30 |
1.00 |
1.00 |
1.000 |
- |
0.64 |
优质无烟煤 |
90.0 |
2.5 |
2.00 |
3.5 |
0.25 |
0.600 |
1.10 |
0.64 |
沥青焦 |
97.0 |
0.5 |
0.50 |
0.5 |
0.4 |
0.700 |
0.20 |
0.55 |
2、增碳剂的应用
选用增碳剂时,一般都应该注意以下几点。
(1)固定碳和灰分的含量
固定碳和灰分是增碳剂中此消彼长的两个对立参数,也是影响增碳效率的两个最重要的参数。增碳剂中的固定碳含量高、灰分低,则增碳效率高,反之则增碳效率低。由于生产条件下影响的因素很多,很难严格评定两参数各自对增碳效率的影响。
灰分高,对增碳有抑制作用,而且还会使炉渣量增多,从而延长作业时间,增加电耗,增加冶炼过程中的劳动量。
从增碳效率考虑,当然希望增碳剂的固定碳含量高一些、灰分低一些,但同时也要考虑生产成本的因素和对铁液质量的影响。
(2)加入方式的影响
增碳剂的加入方式对增碳效率也有很大的影响。
装料时将增碳剂与炉料混匀,置于感应电炉的底层和中部,增碳效率较高。无心感应电炉熔炼灰铸铁时,铸铁的目标成分、各种炉料的配比和其他多种工艺因素,都会影响增碳剂的增碳效率。不同增碳剂的增碳效率大致可参见表4。
表4 炉内加入不同增碳剂时的增碳效率(增碳剂粒度:1.5~9mm)
增碳剂 |
固定碳含量 (%) |
灰分 (%) |
硫含量 (%) |
增碳效率 (%) |
煅烧硬沥青 |
99 |
0.40 |
0.25 |
95~97 |
低硫煅烧石油焦 |
99 |
0.30 |
0.42 |
95~97 |
中硫煅烧石油焦 |
98 |
0.48 |
1.50 |
93~95 |
沥青焦 |
94.3 |
4.30 |
0.37 |
88~91 |
沥青 |
87 |
11.30 |
1.25 |
63~67 |
出铁时在浇包内加增碳剂,然后冲入铁液,增碳效率比在炉内加入者低得多。美国有人在浇包内加入不同增碳剂进行过对比试验,其要点如下:
熔炼的铸铁是低碳当量铸铁,目标成分是:C 2.55%;Si 1.7%;Mn 0.4%。
出铁时,铁液温度为1510~1530℃。
增碳剂加在浇包内,不同增碳剂的增碳效率大致可参见表5。
表5 在浇包内加入不同增碳剂的增碳效率(增碳剂粒度:1.5~6.5mm)
增碳剂 |
鳞片石墨 |
电极碎屑 |
粒状碳制品 |
无烟煤 |
焦炭 |
灰分 (%) |
0.1 |
0.3 |
0.6 |
5.12 |
11.3 |
增碳效率(%) |
76 |
52 |
48 |
48 |
32 |
(3)增碳剂中的硫含量
熔炼球墨铸铁时,应采用硫含量低的增碳剂,虽然低硫增碳剂的价格高,但却是必需的。
熔炼灰铸铁时,则宜采用硫含量较高的增碳剂。这样,不仅可以降低生产成本,而且还可以利用其所含的硫,增强铁液对孕育处理的回应能力,得到冶金质量高的铸件。在这种条件下,片面地追求增碳剂“质量高”而选用低硫的品牌,不仅增加生产成本,而且还有负面影响。
(4)增碳剂中的氮含量
灰铸铁中含有少量的氮,有促成珠光体的作用,有助于改善铸铁的力学性能。如果氮含量在0.01%以上,则铸件就易于产生“氮致气孔”。
废钢中的氮含量高于铸造生铁。用感应电炉熔炼铸铁时,由于炉料中所用的铸造生铁锭少、废钢多,制得的铸铁中氮含量会相应较高。
此外,由于炉料中使用大量废钢,必须用增碳剂,而大多数增碳剂中氮含量都比较高,这又是导致铸铁中氮含量增高的另一因素。
近十多年来,随着感应电炉的应用不断增多,增碳剂中的氮含量日益受到重视。为避免铸件产生气孔缺陷,感应电炉熔炼铸铁时所用的增碳剂,一定要选购含氮量低的品种,如有可能,应核查增碳剂的氮含量。当前的困难在于:分析增碳剂中的氮含量,尚缺乏简便而准确的方法。
(5)其他工艺因素对增碳效率的影响
除增碳剂中的固定碳含量和灰分对其在铸铁中的增碳效率有重要的影响外,增碳剂的粒度、加入的方式、铁液的温度以及炉内的搅拌作用等工艺因素都对增碳效率有明显的影响。在生产条件下,往往是多种因素同时起作用,难以对每一因素的影响作准确的说明,需要在具体生产条件下通过试验来优化工艺。
出铁时将增碳剂加入浇包内,然后冲入铁液,增碳效率与铁液的温度有关。在正常的生产条件下,铁液温度较高,则碳较易溶于铁液,增碳效率因而较高。
一般说来,增碳剂的颗粒小,则其与铁液接触的界面面积大,增碳的效率就会较高,但太细的颗粒易于被大气中的氧所氧化,也易于被对流的空气或抽尘所致的气流带走,因此,增碳剂颗粒尺寸的下限值以1.5mm为宜,而且其中不应含有0.15mm以下的细粉。
颗粒尺寸的最大值,应该以能在作业时间内溶入铁液为度。如果增碳剂在装料时随金属炉料一同加入,碳与金属的作用时间长,增碳剂的颗粒尺寸可以较大,上限值一般可为12mm。如果在出铁时加入铁液中,则颗粒尺寸宜小一些,上限值一般为6.5mm。
搅拌有利于改善增碳剂和铁液的接触状况,提高其增碳效率。在增碳剂与炉料一同加入炉内的情况下,有感应电流的搅拌作用,增碳的效果较好。向包内加增碳剂时,增碳剂可先置于包底,出铁时使铁液直冲增碳剂,或连续地将增碳剂投向液流,不可在出铁后投放在浇包内的液面上。
增碳剂如被卷入炉渣中,就不能与铁液接触,当然会严重影响增碳效果。因此,如采用在出铁时增碳的工艺,应特别注意避免渣、铁混出。
友情链接 友链交换添加QQ:2694467624 其他问题请咨询网站客服