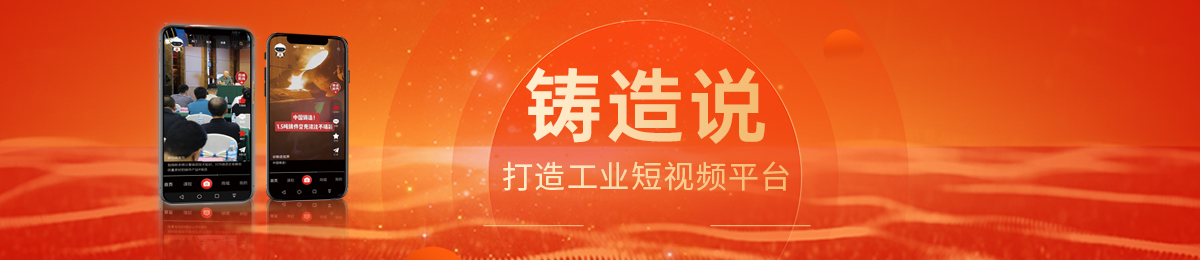
您好, 欢迎来到百铸网! 热线电话:400-8088-177 企业邮箱:[email protected] 注册|登录
2016-03-21来源:暂无数据
1缩孔和缩松是球墨铸铁的主要缺陷
工业上的铸铁是一种以铁、碳、硅为基础的复杂的多元合金,其碳的质量分数一般在2.0%~4.0%的范围内变动。纯铁在加热或冷却过程中还有磁性的转变,温度高于770℃时无磁性,温度低于770℃时有磁性。球墨铸铁是指用球化剂处理铁液后,石墨呈球状的铸铁。缩孔和缩松是球墨铸铁的主要缺陷。
1.1缩孔和缩松的特点
缩孔和缩松在球墨铸铁中要比普通灰铸铁中更为普遍。要防止它们,就必须给予更多的注意和控制。能够明显看出的、尺寸较大而又集中的孔洞叫缩孔,不易看清的、细小分散的孔洞叫缩松。
大多数在铸件热节的上部产生缩孔。在铸件热节处、在缩孔的下方往往有比较分散的缩松。但是,对于一些壁厚均匀的中心,或者是在厚壁的中心部位,也可能出现缩松。
有些缩松的体积很小,只有在显微镜下才能被发现。这种缩松呈多角形,有时连续,有时断续,分布在共晶团边界,这种缩松叫显微缩松。
球墨铸铁缩孔与缩松的体积比普通灰铸铁、白口铸铁和碳钢的都要大。球墨铸铁的缩孔与缩松的体积有可能是普通灰铸铁的3~4倍,或者更多。
1.2球墨铸铁缩孔与缩松增大的原因
经过球化处理后,球状石墨便会立即在铁液中析出,并且,随着温度的逐步降低,铁液中的石墨球逐渐长大。石墨析出和长大的过程,伴随有液态金属的膨胀。
铸铁共晶转变温度是1153℃(Fe-C稳定态)或1147℃(Fe-Fe3C亚稳定态)。球墨铸铁以离异共晶的方式进行共晶转变。其凝固方式是内外几乎是同时进行的粥样凝固,因而容易形成显微缩松。
由于呈粥样凝固,铸件在共晶转变期间要持续很长时间,球墨铸铁的共晶凝固时间可比普通灰铸铁延长一倍还要多。因此,导致共晶转变的石墨化膨胀增大。
在共晶凝固期间,由于粥样凝固决定了铸件表面的凝固层很薄,以致不能建立起足够强度的凝固外壳,以抵抗共晶凝固期间产生的石墨化膨胀,致使铸型内壁向外移动。在铸型刚度不够的情况下,使型腔尺寸增大,由此导致缩孔和缩松的体积进一步增大。
铁液经过球化处理后,原有的氢、氧、氮和CO气体含量减少,铁液得到净化,致使外来的核心减少。并且,铁液的过热温度越高,净化的程度也越高,由此导致的过冷倾向也更加剧。此外,球化元素镁和稀土均能与碳形成碳化物,由此减小了石墨化程度,加大了收缩倾向。
2防止产生缩孔和缩松的措施
2.1铁液成分
碳、硅、锰、稀土、镁的含量必须适当。含碳量高,可使缩孔和缩松的倾向减小,但含碳量过高,会产生石墨漂浮。对于薄壁铸件来说,碳、硅含量低时,易产生游离碳化物。对于厚壁铸件,可采用较低的碳量,并适当增加硅量。锰易形成碳化物,容易促使形成缩孔和缩松。为此,应当力求降低含锰量,尤其是对于铸态铁素体球墨铸铁,更应如此。
在保证球化的前提下,不使镁和稀土的残留量过高。
2.2铁液状态
缩孔和缩松倾向小的铁液,所具有的冷却曲线的斜率应较小。共晶凝固时的膨胀要小。为此,要满足的条件是:
①冷却速度慢。
②碳当量高,析出石墨的倾向大。
③铁液中有效石墨核心数量多。
④良好的孕育效果。
2.3浇注温度
为了防止产生缩孔和缩松,就要使液态收缩量减小,浇注温度低是有利的。但是,对于薄壁(10mm)铸件来说,容易出现碳化物。此时,采用冒口补缩难以发挥作用。因此,适宜的浇注温度还是取决于铸件结构与铸件壁厚。
2.4浇注系统
采取顺序凝固方式,对于铸件、冒口、冒口颈、内浇道、和横浇道的设计与安装,以及外冷铁的设置和必要时采取金属型等,均是行之有效的防止缩孔和缩松的措施。
2.5铸型刚度
对于湿砂型来说,铸型的刚度要求在90(B型硬度计)以上,希望能达到40MPa的抗压强度。此外,砂箱的紧固也十分重要的。对于金属型覆砂(覆砂厚度8mm左右)以及用自硬砂制作大型铸件时,可以实现无冒口铸造。此时,要满足的条件是:
G≥α1+α2+β
式中 G —由碳的石墨化而引起的铁液膨胀量;
α1 ——铁液的液态收缩;
α2—— 凝固收缩;
β —铸型膨胀量。
自硬砂制作大型铸件,生产效率低,适宜用于小批量生产。在大批量生产中,湿砂型工艺的致命弱点是:铸型的刚度不均匀,有的部位,如垂直面的刚度就往往难以达到90(B型硬度计)以上的要求。目前用得最多的是金属型覆砂造型方法。该方法铸型刚度好,铸型膨胀量小,防止缩孔和缩松的效果好。
3金属型覆砂造型方法和缺点
3.1金属型覆砂造型方法是在粗成形的金属型(称为铁型)内腔覆上一薄层砂而形成铸型的一种铸造工艺。见下图:
本地图片,请重新上传
图1金属型覆砂造型
3.2金属型覆砂造型方法的缺点
4球墨铸铁的新型造型方法磁力紧实造型。为了克服金属型覆砂工艺存在的缺点,笔者提出了适用于球墨铸铁的新型造型方法磁力紧实造型,具体做法是将垂直分型的壳型铸型垂直立于截面积上大下小的砂箱中,周边用磁性金属丸充填,浇注铁液结束至铁液凝固结束期间砂箱底部的磁铁工作,磁性金属丸在重力和吸力的作用下,在截面积上大下小的砂箱中,其向下运动的趋势将中间垂直放置的壳型铸型挤紧,增强了铸型的刚性。
本地图片,请重新上传
图 磁力紧实造型方法整体结构主视图
附图说明
附图中壳型铸型1、磁性金属丸2、截面积上大下小的砂箱3、底板4、磁铁5。
本技术的优点是:
①铸型刚度好,铸型膨胀量小,防止缩孔和缩松的效果好。
②由于铁丸之间的间隙透气性好,并且在砂箱壁设置有带网格的排气孔,排气通畅,防止产生气孔的效果好。
③生产线十分方便组织小批量、多品种生产,如要更换铸件品种时,只需更换壳型铸型就行了,这样可以减少投资,降低成本。
④铁液凝固结束后砂箱底部的磁铁即停止工作,吸力解除,这时磁性金属丸仅仅受到重力作用下,有利于铸件的收缩和减小铸造应力,减小了铸件冷裂的倾向,提高了产品的可靠性。
⑤磁力紧实铸造造型方法砂箱的通用性强,结构简单,投资少、成本低;而金属型覆砂工艺的砂箱只能适用于某种铸件,并且内腔与铸件形状相似,结构复杂,投资大、成本高。
⑥每次生产消耗和排放的是壳型铸型,其余的如磁性金属丸等可以重复使用,属绿色生产。
5结论
5.1磁力紧实铸造造型方法克服了现有的金属型覆砂工艺柔性差、排气困难、工作环境温度高等缺点,具有高的铸型刚度,排气通畅,柔性好,便于组织小批量、多品种的生产。
5.2磁力紧实铸造造型方法砂箱的通用性强,结构简单,成本低;而金属型覆砂工艺的砂箱只能适用于某种铸件,并且内腔与铸件形状相似,结构复杂,成本高。
5.3磁力紧实铸造造型方法磁性金属丸等可以重复使用,排放少,属绿色生产技术。友情链接 友链交换添加QQ:2694467624 其他问题请咨询网站客服